Journal Papers |
Book Chapters |
Conference Proceedings
Paper
Topic Code:
|
CP =
conjugated polymer
cell = cell-based sensors
DEA = dielectric elastomer
EIT = electrical impedance tomography
FO = fiber optic sensor
LC =
liquid crystal
|
MEMS = microfabrication
nast = nastic actuators
PLED = polymer light emitting diode
SAM = self-assembled monolayer
sens = misc. sensing |
Click on Year to sort by year, and click on Code to sort by the paper topic codes given above.
Year |
Code |
Citation |
2024 |
EIT
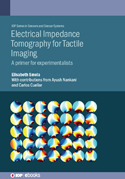
|
E. Smela (with contributions by A. Nankani and C. Cuellar)
Electrical Impedance Tomography for Tactile Imaging: A Primer for Experimentalists, OP Series in Sensors and Sensor Systems (IOP Publishing Ltd, Bristol, UK, 2024)7.
Can be found on the website of the Institute of Physics, IOP.
Electrical impedance tomography (EIT) is a technique employed in tactile sensing to create an image of impedance changes within a continuous sensor using electrodes placed only at the perimeter. This is advantageous for soft sensing 'e-skins' being developed for applications such as robotics and human–machine interactions. EIT was originally developed for medical diagnostics and has more recently been adopted for tactile imaging, which has distinct requirements and challenges. This book explains the fundamentals of EIT at a basic level, without requiring a high level of mathematical expertise, making it an accessible text for students and newcomers to the field. It also covers applications and challenges of the method, recent developments, and practical implications.
Chapters:
1. Tactile imaging with electronic skins (free to read)
2. Use of electrical impedance tomography for tactile imaging
3. Simulation conditions and performance metrics
4. In layperson's terms, how does electrical impedance tomography work?
5. Effects of the hyperparameter
6. Noise
7. Experimental decisions (includes two papers, "EIT for tactile sensing: considerations regarding the injection-measurement pattern" and "EIT for tactile sensing: considering artefacts in hyperparameter selection" - see the Journals page)
Back matter (appendices)
Part of the IOP Series in Sensors and Sensor Systems. |
2017 |
sens |
H. A. Bruck, E. Smela, M. Yu, Y. Chen, and J. Spokes
in Mechanics of Composite and Multi-functional Materials, Vol 7: Proc. An. Conf. Experimental and Applied Mechanics, edited by W. Ralph, R. Singh, G. Tandon, P. Thakre, P. Zavattieri, and Y. Zhu, 2017.
Can be found on the webite of Springer.
A challenge in fabricating compliant electrical sensors for various applications, such as wearable electronics, has been the lack of compatible connection concepts that are reliable and can support large levels of force without failure. Recently, we have developed compliant, carbon-based strain and thermal sensors using nanosized exfoliated graphite (EG) dispersed in latex that are highly deformable (>50 % strain) and piezoresistive. They undergo large changes in electrical resistance, resulting in highly sensitive strain (1x10-3/µstrain) and thermal (1x10-3/K) measurement sensors. Such compliant sensors are typically attached to external wiring using conductive silver epoxies or paints. However, the silver epoxy and the metal wires are rigid, and they detach from the compliant sensor at low load levels. By using micronsized braided carbon fibers instead of metal, and a carbon-based composite instead of silver epoxy, a mechano-electrical interface to the sensor is created that has a significantly higher load bearing capacity than achieved with metal wires, with an inherent electrical resistivity of only 1.7x10-3 O-cm. The resulting sensor is similar to a sensory nerve receptor where the percolated network of nanosized EG act as “receptors,” while the micro-sized carbon fiber acts as the sensory ganglion attaching to the central nervous system. The resulting “biologically inspired” multi-scale strain and temperature sensor has advantages in addition to durability, including amenability to additive manufacturing processes, ease of fabrication, and scalability. We also demonstrate the ability to use the new sensing material to make “sensing gloves” that could potentially be used in applications such as recording signals during manual tasks by human hands or for providing sensing capability to robotic hands. |
2009 |
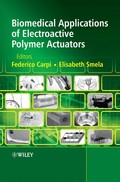 |
F. Carpi and E. Smela Biomedical Applications of Electroactive Polymer Actuators
John Wiley & Sons Ltd., 2009.
Electroactive polymers (EAP) are a family of "smart materials" that possess an attractive combination of
intrinsic electromechanical transduction capabilities with the mechanical flexibility, processing
versatility, and low cost that are typical of polymers. As a result, EAP actuators are being studied as
candidate materials for "artificial muscles". This book describes work toward biomedical applications of
the most technologically mature classes of EAP, namely polymer gels, ionic polymer metal composites,
conducting polymers, piezoelectric/electrostrictive polymers, and dielectric elastomer actuators. |
2009 |
CP |
E. Smela
in Biomedical Applications of Electroactive Polymer Actuators, edited by F. Carpi and E. Smela John Wiley & Sons, Ltd., 2009.
Robots that swim in the bloodstream, scissors that take a biopsy from within a blood vessel deep inside
a kidney, tapping fingers that measure the hardness of cells to distinguish cancerous from normal
tissue, and smart pills that dispense drugs in concentrations that change with the body's needs -
these are among the future technologies that have been envisioned by engineers and doctors for
minimally invasively diagnosing and treating patients. However, working on the micro-scale like
this will require micro-scale tools (microelectromechanical systems, or MEMS). In this chapter, we review some of the exciting prototype micro-scale biomedical devices that have been demonstrated in the laboratory. |
2006 |
CP |
G. M. Spinks and E. Smela
in Handbook of Conducting Polymers, 3rd ed., edited by T. A. Skotheim and J. Reynolds, p. Chapter 14 (Taylor & Francis CRC Press, Boca Raton, 2006)
In many respects, conjugated polymers are well-suited for micro-electro-mechanical systems (MEMS) and other micro-devices. The versatility of function makes conjugated polymers potentially useful for micro-actuators, micro-sensors, and micro-energy sources (such as batteries). Furthermore, the speed of micro-sized conjugated polymer devices can be greatly enhanced over macro-scale devices since ion transport distances are small and surface areas are large. In addition, the wide range of patterning methods suitable for conjugated polymers enables straightforward micro-fabrication of these materials. This paper reviews the inherent advantages of conjugated polymers for micro-devices and describes some of the demonstration devices already constructed. Some future directions, including challenges and the possible development of nano-scale conjugated polymer devices, are also discussed. |
2001 |
CP |
E. W. H. Jager, E. Smela, and O. Inganäs Chapter 13,
in Communications Through Virtual Technology: Identity, Community, and Technology in the Internet Age, Vol. 1, edited by G. Riva and F. Davide (IOS Press, Amsterdam, 2001)
Conjugated polymers actuators can be operated in aqueous media,
which makes them attractive for laboratories-on-a-chip and applications in
physiological conditions. One of the most stable conjugated polymers under
these conditions is polypyrrole, which can be patterned using standard
photolithography. Polypyrrole-gold bilayer actuators that bend out of the plane
of the wafer have been microfabricated in our laboratory. These can be used to
move and position other micro-components. We review the current status of
these microactuators, outlining the methods used to fabricate them. We describe
the devices that have been demonstrated as well as some potential future
applications. |
1996 |
CP |
E. Smela, O. Inganäs, and I. Lundström
in Molecular Manufacturing, Vol. 2 of the series Electron. Biotechnol. Adv. (EL.B.A.) Forum Ser., edited by C. Nicolini, p. 189-213 (Plenum Press, New York, 1996)
A review with many refs. on microelectronic devices from conducting polymers prepd. using silicon microfabrication methods.
|
Journal Papers |
Patents |
Book Chapters |
Conference Proceedings
|